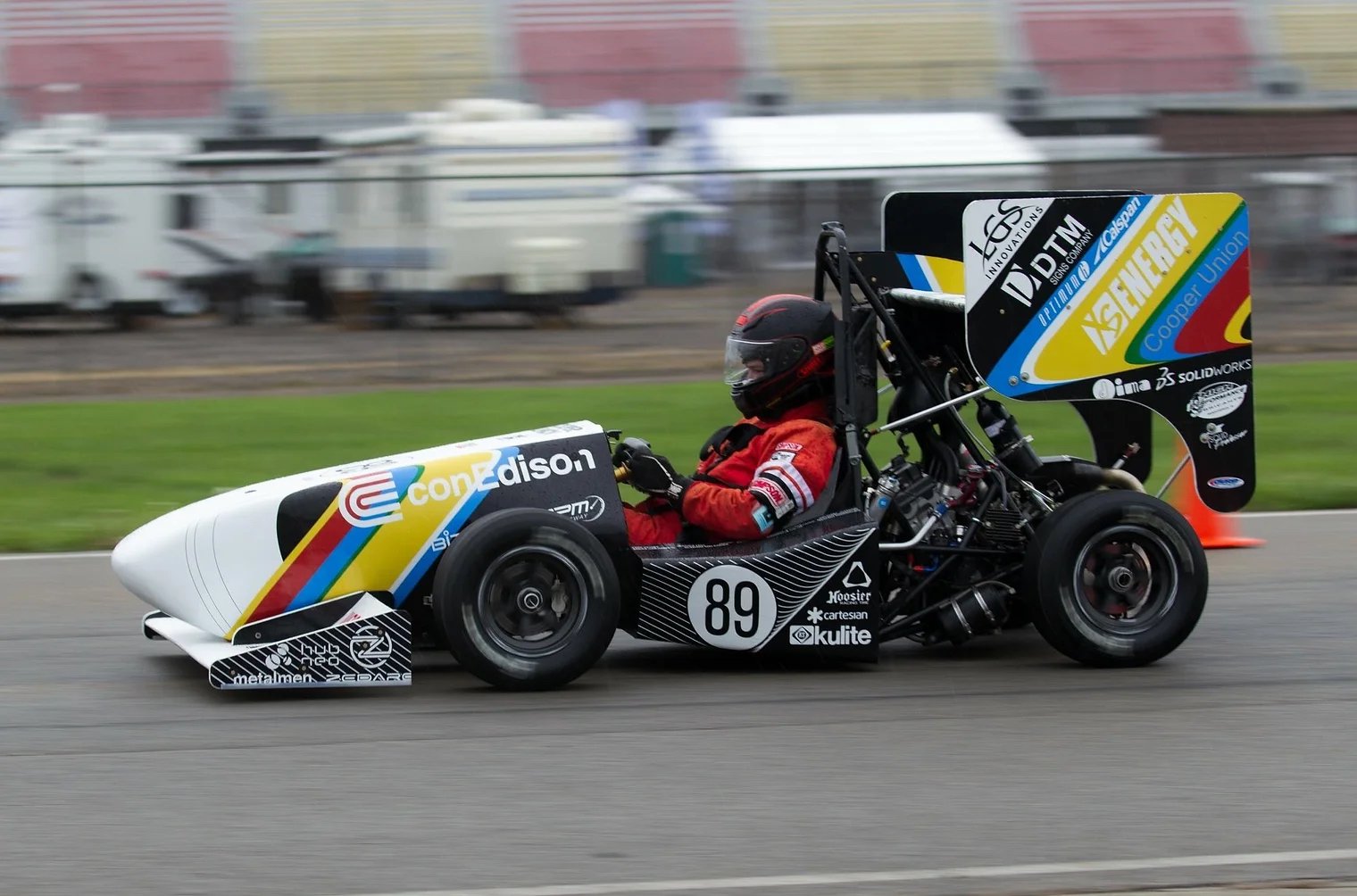
FSAE Impact Attenuator
To adequately determine if the carbon fiber would exceed the performance of the old aluminum IA design, the aluminum IA had to be made and tested.
According to 2018-2019 FSAE regulation T3.21.2, the IA assembly must decelerate a vehicle at a rate not exceeding 20 g's average and 40 g's peak, absorbing at least 7350 Joules, when mounted on a vehicle with a mass of 300 kg and impact velocity of 7.0 m/s.
Initial tests with only 10% of the rated impact energy and 1/2 of the layers of honeycomb yielded a peak acceleration of only 5 gās.
Drop tests with the dynamic test rig were performed on both the honeycomb aluminum IA and the fabricated carbon fiber IA. The final shape of the carbon fiber part was derived through smaller tests with various cardboard prototypes that fit within the geometric constraints given by competition rules. Once the shape was determined, it was cut out of foam with a hot-wire cutter and then vacuum molded with 7 layers of twill-weave carbon fiber and epoxy.
The impact attenuator (IA) is a deformable, energy absorbing device responsible for damping the forces experienced by the car frame and driver during a head-on collision. In previous years, the impact attenuator was made from layers of honeycomb aluminum attached to the nose of the car. This material, structure, and position was advantageous for effectively absorbing an impact without greatly increasing the weight of the car. However, the FSAE team was interesting in experimenting with lighter materials, specifically carbon fiber, for the IA material and determining if it could match or exceed the performance of the aluminum honeycomb. I investigated the viability of this new material choice in a team with other high school students and a member of the Cooper Union Motorsports team for the summer STEM program.
To simulate a head on impact without actually driving the car into a wall, a dynamic testing rig was used to drop weights onto the IA assembly. The testing rig consisted of a ceiling mounted winch that raised and released sets of 50 lb weights on a cable guided platform. To achieve 7350J and a speed of 7 m/s on impact, six 50 lb weights were released from a height of 2.5 meters. An accelerometer was mounted onto the drop-platform to measure the deceleration and a high-speed camera was used to analyze how the IA deformed during impact.
Final testing was performed with the full weight to simulate the FSAE standards. During testing a high-speed camera was used to visualize how and where the carbon IA failed first. While the footage was not usable, the accelerometer data indicated that the carbon IA was not feasible as it exceeded the 40g deceleration limit. In other words, it was too stiff and would not cushion the rider enough. The team still uses an aluminum honeycomb IA design.